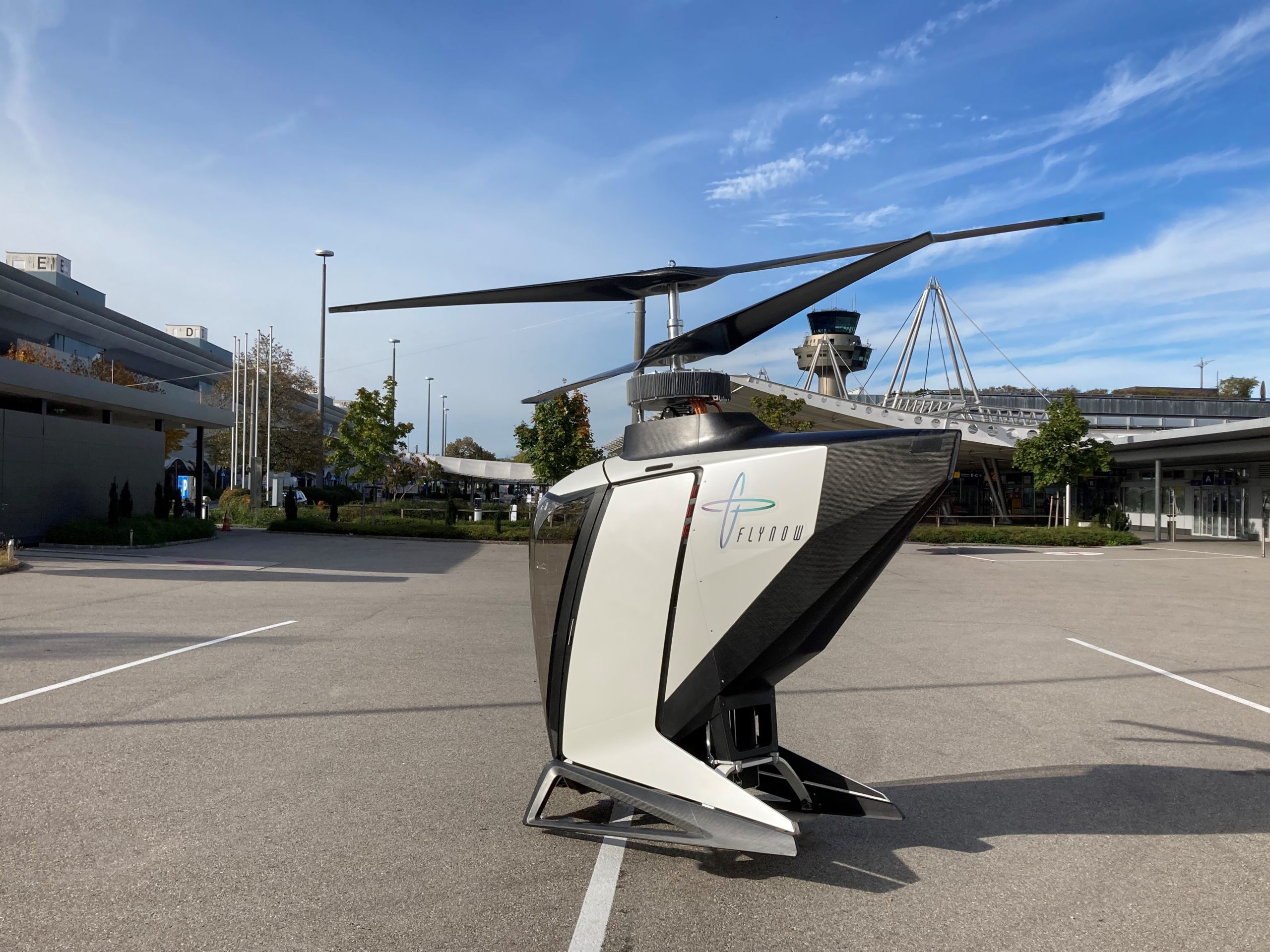
A view by Jürgen Greil, CEO, FlyNow Aviation, on Michael Halaby`s article, which first was published in the May 2023 edition of Royal Aeronautical Society’s AEROSPACE magazine.
Mr Michael Halaby from the Royal Aeronautical Society describes in an article published in Aerospace magazine some of the most challenging problems eVTOLs face to meet suggested requirements and his conclusions are all more than viable. As an expert in the aviation industry for many decades he knows the pain points and issues the industry has been trying to tackle since the beginning of commercial flight. The mentioned applications for a first success are all valid and will be applied, but this does not mean, that affordable and available “air taxis” are not also possible, if certain requirements are fulfilled, respectively assumptions, based on existing constraints, are altered.
The main purpose of eVTOL will be to substitute ground transportation systems, mostly cars. The cars, buses and trains powered electrically however, are also susceptible to getting stuck in traffic jams as their conventional counterparts since they are dependent on the same infrastructure. In addition, it is important to note that producing electric alternate vehicles need the same number of resources (or even more) to produce them. In general ground infrastructure is not only very expensive to build and maintain, but also seals the ground with all the resulting problems and additional costs.
The automotive industry is the only form of mobility whose total ecosystem is making money and in comparison, existing sea-, air- & rail transport systems is not subsidised. (Just to emphasize the meaning of Subsidy: This means that neither interest is paid nor is there any repayment) It is important to understand that exclusive car brands, despite their high prices, usually earn no or less money compared to volume models, which cross-subsidize them within a group.
But this was not always the case. In the dawn of the automotive industry, cars were extremely expensive and only a chosen few were able to afford them and willing to risk their lives to drive them. In a figurative sense, the prerequisites for the operation of aircraft for 3D mobility are today similarly inhibiting, as during 1865 and 1896 when a man with a red flag (Locomotives Act 1865 also known as the Red Flag Act in UK) had to walk in front of each car to warn the other traffic that a horseless carriage was coming down the road.
Among others it was Ford with the “Model T” and Volkswagen with the “beetle” who reduced the production cost by industrializing, to a level that the average person could afford them. This was the breakthrough for individual mobility and made the car the world´s dominant means of transportation.
This also set the governments to invest in the construction of the necessary infrastructure since they had the support from the tax-paying population.
FlyNow Aviation is clearly positioning itself in the volume segment to be a game changer in the aviation industry, which has not yet managed to advance into the financially attractive area with its quantities.
To achieve this kind of transition for 3D-mobility, an air vehicle must meet the requirements of the potential customers under the technical constraints associated with electric mobility. Since people are usually commuting by themselves and most inner urban and last mile deliveries are smaller than 1m3, lighter than 200kg and below 50km per leg, FlyNow is focusing on a modular family of aircraft consisting of a cargo and a single and twin seater version. All the derivates share the same drivetrain with a battery at the bottom of the cabin and coaxial rotor propellers, each driven by one of the two four times redundant electric motors positioned in one housing, mounted on top of the cabin forming a tilting head mechanism via a gimbal joint. This leads to the simplest form of controlling the six degrees of freedom necessary for safe control of an aircraft, in a three-dimensional space.
Due to the positioning of the passenger(s) or cargo and the packaging of all the components and modules, in such a way that the Center of Gravity is below the drive train axis, this allows very simple cabin topology which avoids almost all bending movements. This package in combination with the customer focused requirement, fires a downward spiral leading to a much smaller battery pack and therefore leads to an exceptionally light aircraft. This in return reduces the necessary power and reduces the size of the drivetrain.
Regarding efficiency, besides low weight described above, a general valid aerodynamic principle is that, accelerating a large amount of air at moderate speeds is always more efficient than accelerating a small mass of air at high speeds to achieve the same level of thrust. This can be observed in engine applications, which are highly cost-efficient passenger aircraft. These usually have engines with very large fan diameters to move large volumes of air at moderate cruising speed. The same applies to propellers and helicopter rotors: the larger the diameter and the lower the speed and disc loading, the higher the efficiency and the lower the noise emissions. Therefore, FlyNow modular family of cargo and passenger VTOLs, which consists of a large low-frequency rotor assembly, is the most efficient, quietest and, due to its safety-relevant topology, the most reliable in this field.
This technological approach of FlyNow allows a sales price of less than EUR100,000 without taxes per PAV with an attractive profit like the most successful car manufacturers. A comparison with the automotive industry could help to classify these figures: in 2019, Bugatti, Lamborghini, Ferrari, and Bentley, which are positioned in percentage terms, with similar production figures to our competitors, had a sales volume of around 26.000 units. Mercedes, BMW and Audi together had more than 6.200.000 units, which corresponds to a 1: 238 relationship.
The FlyNow project aims at a quantity of 10,000 units per year in the first expansion stage of production, in terms of this, competitors have a volume of less than 100 units per year, analogous to the automotive industry, which is increasingly confirmed by the competitors. This mirrors Mr. Halaby´s assumptions!
To be able to realize a meaningful air traffic over cities, take-off and landing hubs are required near or on the most frequented places or buildings. The size of these take-off and landing hubs results on the one hand from the size of the eVTOLs and their “stackability” on the ground as well as their noise emissions. It speaks for itself that the generated noise cannot be higher than the “background noise”, which is common in cities today. If the advantages of UAM concerning speed, comfort, safety, noise, and cost in comparison to ground based transport become obvious then landing fees will be in a magnitude of parking fees, since landing hubs will be built and maintained by many operators, both public and private.
If a pilot is needed to fly an eVTOL then there is obviously no business case, since the labour cost for pilots, but also their availability plays an important role, because if 3D mobility is to significantly replace ground-based traffic, the sheer number of necessary pilots will not be available. Pilots are a rare breed, and it takes a lot of time, money, and effort to become one and to stay current.
But this does not mean that it is necessary to fly autonomously, since the effort in terms of sensors and software is much too expensive and time-consuming and makes the certification process at least delayed, if not impossible. This is true for ground-based means of transport as well as eVTOLs. But the big advantage in the aviation industry is that autopilots have been known and used for many decades. And that’s exactly what it takes to handle automatic flights without a pilot on board to transport cargo and passengers. For the automation of advanced air mobility, air traffic management has to be adapted to manage routes, ensure overall safety, and provide flexibility for passenger mobility and cargo transport.
It is true that the production costs are highly dependent on the size, but also on the complexity, the efficiency, the materials used and the resulting weight of the vehicle. The simpler the concept, the higher the efficiency and the lower the weight of such an aircraft the longer the replacement cycles as well as the time between overhaul (TBO) of the components and the lower the operation costs.
So far, the energy density of the energy carrier as well as the associated energy converter has not only increased with every technological leap from hay/horse via coal/steam engine to oil/internal combustion engine, but also the type of means of transport (carriage, train, car). Significantly lower energy density of batteries can´t be compensated by the higher efficiency of the electric motor, so there is no way around a drastic reduction in the weight of the means of transport, if affordable costs for individual mobility are to be maintained. This applies both to the means of transport itself, and to the infrastructure necessary for it. 3D mobility can make an important contribution to achieving this goal, if the required aircraft and associated operating conditions can be realized in such a way that ground-based traffic can be meaningfully substituted.
Ground-based means of transport have reached their limits in many ways and in many places around the world. Starting to transport urgent goods, medical and life saving equipment and other important things help to implement new means of transport, mitigates technical and financial risks, and proves the benefits to the common public. This is going to create the necessary market pull for individual 3D mobility contributing to mitigate the current traffic problems if some boundary conditions are adapted, like the mechanisms used that helped the automobile to change the world to better, more than 100 years ago.