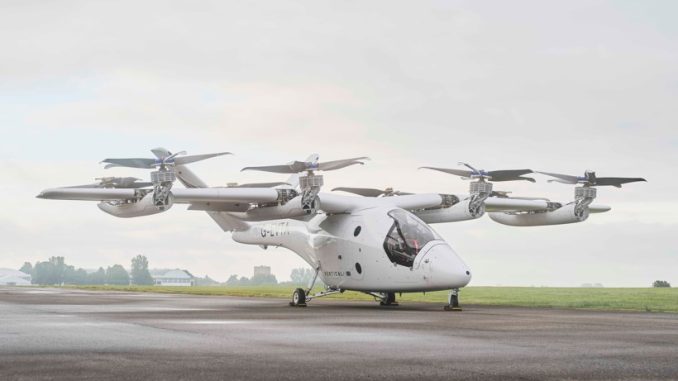
The next-generation VX4 is more powerful than the previous full-scale prototype, with a 20% increase in the power to weight ratio, enabling the aircraft to reach speeds of up to 150mph – the certification aircraft’s intended cruise speed, says the company.
The aircraft has been designed and built alongside global aerospace partners, including GKN Aerospace, Honeywell, Hanwha, Molicel, Leonardo and Syensqo. It features Vertical’s next generation propellers and new proprietary battery technology, designed and manufactured at its Vertical Energy Centre near Bristol.
The new VX4 prototype has completed systems and aircraft testing and commissioning. Vertical is now working closely with the UK Civil Aviation Authority (CAA) as it evaluates the engineering, design, test data and aircraft ahead of issuing a Permit to Fly, effectively conducting a “mini certification” programme. Vertical will then begin a flight test programme at the Vertical Flight Test Centre, with a focus on achieving piloted flight.
Vertical is currently developing an identical full-scale prototype which will accelerate the VX4’s flight test programme and demonstration capability. The company will take flight test learnings from both prototypes into the design and development of the certified VX4 model.
Key new features of the latest full-scale VX4 prototype:
- Aerospace partner technology and certification expertise – 60% of the technology and components included on the latest aircraft are from aerospace partners, up from 10% on the previous prototype. This makes it Vertical’s most advanced prototype yet and a step closer to the aircraft that the company will take through to certification.
- First use of battery designed and built for aviation – This battery and powertrain system, developed at the Vertical Energy Centre, is the most powerful and lightest yet, has rapid charge time and multiple backup power sources. The VX4’s batteries are designed to meet the performance, safety, operational and commercial requirements of eVTOL and the first time its own proprietary batteries have been used on a full-scale prototype. The electronics, software and design of the battery have all been developed in house and the new aircraft includes new, more powerful Electronic Propulsion Units.
- Next generation propellers – Vertical’s new proprietary propellers designed specifically for eVTOLs are optimised for low noise and made of carbon fibre composite using a single-shot cure process to maximise integrity. The aerodynamic shape has been specifically designed to maximise performance across both hover and cruise by deconflicting the requirements of each phase of flight.
Stuart Simpson, Chief Executive Officer, Vertical, said “Our goal is to build the safest and most advanced aircraft in this new category of transport. With the new full-scale VX4 prototype, which has been built by combining our own world-leading technology with that from leading aerospace partners, we are well on the way to achieving that goal.
“This is a critical step on our road to certification and commercialisation and, while there is more to do, the support of our partners and our $6 billion order book shows the trust and confidence the industry has in our outstanding product. We are excited to start our robust, test flight programme at our Flight Test Centre as we continue our focus on achieving piloted flight.”
Vertical’s leading aerospace partners:
Piloted flight test programme explainer:
|
For more information